色ムラ
色ムラとは
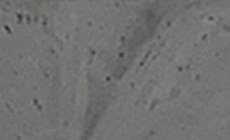
色ムラ見本
色ムラとは、射出成形にて成形品の色に濃淡のムラが出てしまう外観不良のことを指します。
色ムラが発生する要因
ほとんどの場合は、混練不足が要因で成形品に不均一なムラが発生する事が多いです。
別要因では、材料が熱劣化した事が原因で色ムラが発生する場合もあります。
─ 着色剤の種類
着色材は4種類ほどありますが、使用されやすい着色材料を2種類ご紹介します。
❙ マスターバッチ
ペレット状の顔料にナチュラルペレットの2種類を混ぜ合わせて色を出します。
特徴は、価格が安い点と顔料(マスターバッチ)のベースを調整する事で着色濃度を変える事ができます。
ただし、顔料とナチュラルペレットの2種類をスクリュー内で混ぜ込む為、混練性が弱いと色ムラが発生しやすい傾向にあります。
❙ 着色ペレット
既にペレットに顔料が混ぜ込んである材料の事を言い、ナチュラルペレットと混ぜ合わせる必要がありません。
着色ペレット単体で成形する事が出来る為、色ムラが発生しにくいのが最大の特徴です。
ただし、着色ペレットはマスターバッチより価格が高い為、大量生産にはあまり向きません。
色ムラ対策
─ 成形条件出しで改善
❙ 成形温度を上げる
メリット | 温度を上げることで、材料同士がしっかりと溶融され、混ざりやすくなる。 特にマスターバッチを使用している場合は、効果が高い。 |
デメリット | 温度を上げたことにより顔料が熱劣化を起こし、色が変色する可能性がある。 |
❙ 背圧を上げる
メリット | 背圧を高く設定する事で高い混練性を上げる事ができる。 |
デメリット | 背圧を上げ過ぎると計量に時間がかかり、1度の成形にかかる時間(サイクルタイム)が延びてしまう。 |
─ 混練専用の付帯設備を導入
❙ サブフライトスクリュー
メリット | スクリュー内部で混練不足を補う事ができる混練性能が非常に高い事に加え、サブフライト機構により材料が均等に混練され、色ムラの発生を抑制する事も可能になる。 |
デメリット | スクリューの取り換えが必須になるため、費用が高額化になりやすい傾向にある。通常のスクリューよりメンテナンスが大変な難点もある。 |
❙ ミキシングノズル
メリット | 成形機ノズルと取り換えるだけで色ムラを抑制する事が可能になる。また、サブフライトスクリューより安価に導入する事ができる。 |
デメリット | サブフライトスクリューの方が、混練性が高い。 |
解決策 FISAからのご提案
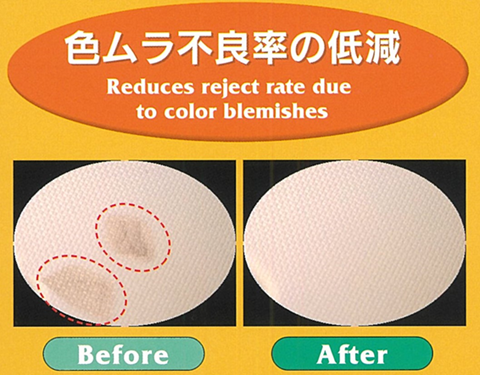
フィーサでは樹脂混錬パーツ『プラムチップ』をご用意しています。
『プラムチップ』は、らせん形状の加工がされたパーツで、 射出成形機のノズルに組み込むことで、分散・合流を繰り返して色ムラを解消します。
また、キャップとボディの間にはさみ込むだけのシンプルな構造で、メンテナンス性も良く、短時間で復旧できます。
プラムチップノズルは無料の貸出ノズルにてお試し頂くことも可能です。